You have no items in your shopping cart.
Before they become a unique staple of a packed city street, manhole covers need to go through a complex production process. From pattern designing to pouring molten iron, the manufacturing of manhole covers is an incredibly laborious yet fascinating task involving patience, preparation, and even a splash of creativity.
Manhole covers might have the duty of keeping pedestrians safe, but factory workers have the even greater responsibility of ensuring that these cast-iron disks are strong enough to withstand harsh conditions and the weight of vehicles. If you’re curious, let’s take a look at how manhole covers are made.
The Manufacturing Process
Cast-iron manhole covers are typically manufactured using a sand mold process in factories known as foundries. The casting process consists of the following four steps:
Making the Pattern
Manhole covers usually have some kind of pattern or image on them, which can represent a city’s culture or an artist’s expression. For the most part, manhole cover molds are either carved out of wood or created out of aluminum using a machine.
Each manhole cover requires two patterns: one for the upward-facing top and the other for the underside. The top is usually a more decorative design, while the bottom side is likely flat. Sometimes, the bottom side features a design, such as a three-dimensional spider web pattern. This provides a greater strength without increasing the weight of the manhole cover.
Preparing the Mold
To begin the molding process, two halves of the manhole model are placed into boxes known as “flasks.” Greensand – wet sand (sometimes mixed with clay, oil, or resin) that is not yet set and therefore still in the “green” state – is then packed tightly into these flasks to create the molds. This process is known as sand molding.
When the patterns are removed, hollow images of both the upper and lower halves of the manhole cover remain imprinted in the sand. These halves can then be assembled into a large metal frame, otherwise known as a “drag flask.”
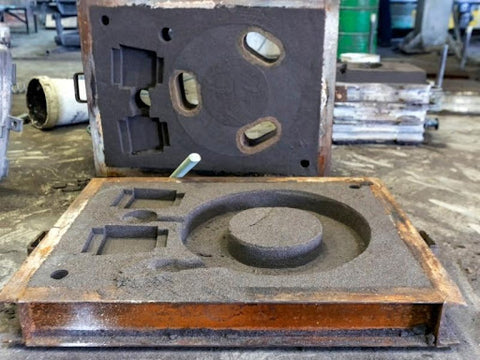
Melting and Pouring
At a foundry, scrap metal can be melted in a variety of different types of furnaces to create a manhole cover. Depending on the metal, melting usually occurs around 2,300 - 2,700 degrees Fahrenheit. Other metals can then be alloyed (mixed in) to the molten iron for the purposes of increasing strength or binding with impurities. This binding creates a waste product called “slag” that floats to the top of the molten iron to be removed.
Foundry workers use a large metal ladle or cauldron to collect the molten iron and pour it into the sand mold through holes in the flask, known as risers. Additional holes act as vents that allow gasses to escape. As the iron casting cools, workers must watch out for any exhaust spurting from the mold and ensure that gasses are not trapped inside, which would cause unwanted bubbles in the casting.
Cooling and Finishing
Typically, molten iron will cool slightly after around an hour and a half – enough to allow foundry workers to remove the molds. It takes about a day for the iron to cool completely. Once the cooling has finished, foundry workers remove the sand using a wire brush or by placing the cooled casting on a vibrating grate.
In the finishing stage, the excess metal that hardened in the pouring chamber, known as the sprue, is removed. As a final step, the surface can be shot-blasted. This helps ensure that the manhole cover is non-slip, rust-free, and will lie completely flat within its frame.
What Will Manhole Production Be Like in the Future?
Although cast iron is extremely economical, other manhole cover materials like steel, plastic, and composite are common in unique settings. Computers may even play a role in the future of manhole covers in the creation of designs and computer-aided manufacturing, called CAD-CAM. This technology allows designers of manhole covers to cut their patterns out of plastic molds by automatic machines. This process will take only a few minutes to manufacture a manhole cover.
While the future of manhole cover production seems promising, present-day manhole covers are equally as interesting. For more information on the manufacturing of manhole covers, take a look at our blog post explaining what makes a manhole cover so heavy.